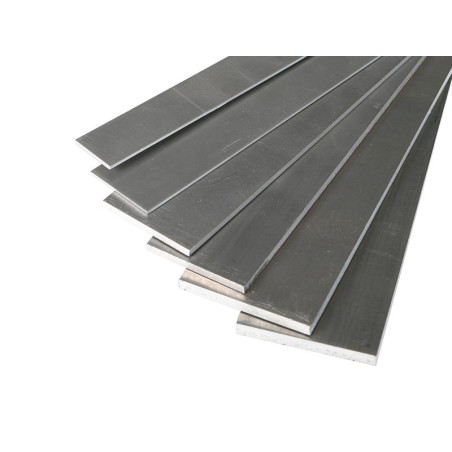
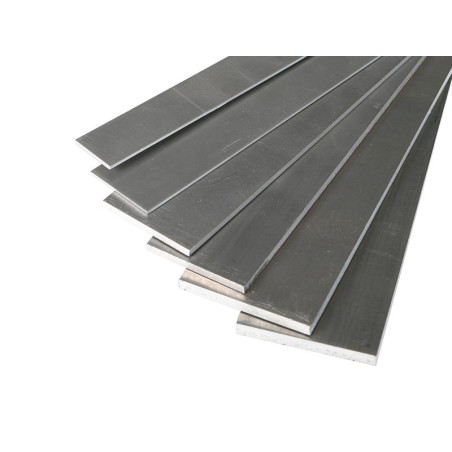
Duralumin flat bar, excellent material for landing gears for flying models, etc....
Dimensions:
Standard:
And, how to "work" and bend duralumin?
Duralumin is an aluminum alloy with a few percent copper content and magnesium and manganese additives, commonly called dural. It used to be a "strategic" material used only in selected industries. Today, it is generally available in the form of sheets, flats, profiles of various cross-sections, rods, shafts of various thicknesses, cross-sections and diameters. Dural is very willingly and widely used by modelers building flying, floating and wheeled models... It is characterized by a favorable structural parameter, i.e. the ratio of strength to specific gravity, which is greater than for steel.
Dural can be machined by hand - cutting and trimming shapes. For machining we use metal saw blades, hairballs for metal, and for complex shapes we use the method of "drilling and punching".
Mechanically - on lathes (turning of shapes) and milling machines (milling of shapes).
Finishing processing. For finishing parts made of dural, metal files rubbed with school chalk are used, which prevents "clogging" of the file. It is not recommended to use rasps for woodworking! And wherever the highest surface quality is required we use waterproof sandpaper of various gradations.
The properties of dural seem to be widely known. However, the matter begins to get complicated when we need to cut a piece out of sheet metal and then bend it or bend it... We start by carefully examining the surface of the sheet metal to get an idea of how it was rolled - rolling marks look like "thin lines". If the cut piece of sheet metal will be used, for example, to make the landing gear shins or the propulsion engine bed of a flying model, then the piece should be cut in such a way (with a finishing allowance, of course) that the bending lines run across the rolling lines. This is not a problem if the landing gear shins are made from flat bar. After the piece is cut out, all edges should be bevelled with a flat semi-smooth (rubbed with chalk). Holes for fixing the shins
in the fuselage and for the wheel axles are routed and drilled only after bending! Now you need to prepare the template on which you will perform the bending or underbending operation. On the bending edges, the radii should be filed. The old rule still applies: the bending radius must be equal to or greater than the thickness of the sheet metal!
First we need to carry out the process of supersaturation, i.e. heating the prepared dural piece, which, after appropriate bending, will be the chassis or bed of the model's drive engine. At home, we carry out the supersaturation process using the "matchstick" method. We place the dural element on the plate of an electric stove or on a gas stove using a cast iron pot pad made of stainless steel. Turn on the electric stove or light the burner of the gas stove... Be sure to take all safety precautions! The heat quickly penetrates the dural element. The surface of the heated element is rubbed with the wood of a match - at first the match scrapes on the surface, which means that the temperature is too low. The moment the dural "catches" the right temperature the match moves smoothly and writes black like a pen. We immediately immerse the heated element in cold water. After cooling, we have about 3 hours to bend.... After that, the dural will be hard again!
compiled by Ludomir Rogalski